JPM Industry had the privilege of attending Maquishoes – Machinery, Technology and Accessories Fair for the Footwear Industry, at the invitation of CTCP – Portuguese Footwear Technology Centre. The event provided a space for reflection and exchange on the main technological challenges shaping the future of the industry.
Representing the company, Guilherme Cardoso, Director of the Intralogistics & Robotics Business Unit, participated in a roundtable discussion alongside representatives from other organisations. The discussion centred on key topics such as process automation, equipment usability, and the role of inspection technology in quality control.
Adapting to Different Geometries and Materials
During the session, Guilherme Cardoso highlighted the main challenges associated with developing a sole deburring machine, a process that remains highly complex due to the wide variety of models and material variability.
According to Cardoso, the key challenges are fourfold:
Diversity of soles, making it difficult to create a universal solution;
Varying morphology and rigidity, which require adaptable equipment;
Process stability, particularly in the automated handling of soles;
Quality of the final result, influenced by factors such as injection quality, materials, and factory environmental conditions.
JPM’s solution involves the integration of artificial vision systems and proprietary adaptive grippers, capable of identifying the optimal picking point and adapting to the sole’s type. This ensures smooth and precise robotic movements throughout the deburring process.
Programming and Usability: The Challenges of Digitalisation
When asked about programming deburring equipment, Guilherme Cardoso acknowledged that any step towards digital transformation presents new challenges for companies, particularly regarding technical skills, process demands, and infrastructure adaptation.
He identified two main challenges:
The industrialisation of new models, which requires rigorous control during moulding and injection to ensure product stability;
The programming of new products, which, while supported by intuitive interfaces and collaborative robotics, still requires specialised knowledge in robotics and industrial vision programming.
In this context, many companies choose to outsource these skills, investing in trusted partnerships while focusing on their core business, where they generate real value.
Automatic vs. Manual Inspection: Technology in Service of Quality
Regarding automatic dimensional inspection, Guilherme Cardoso argued that it should replace manual inspection wherever possible, especially in repetitive tasks that demand precision and consistency. Automation plays a direct role in improving the sustainability and competitiveness of European companies, in an increasingly dynamic global landscape.
Based on JPM Industry’s experience, more than 95% of inspection cases can be automated using artificial vision systems, a technology that has advanced significantly in recent years, both in optics and software. Today, it is possible to achieve precision and detection levels beyond human capability, thanks to the combination of machine learning and artificial intelligence.
The advantages are clear: more stable and predictable processes, higher quality, lower per-unit inspection costs, and increased adaptability to new inspection requirements. Existing limitations, such as complex product shapes or the need for very high cycle times, are gradually being overcome through continuous technological advancement.
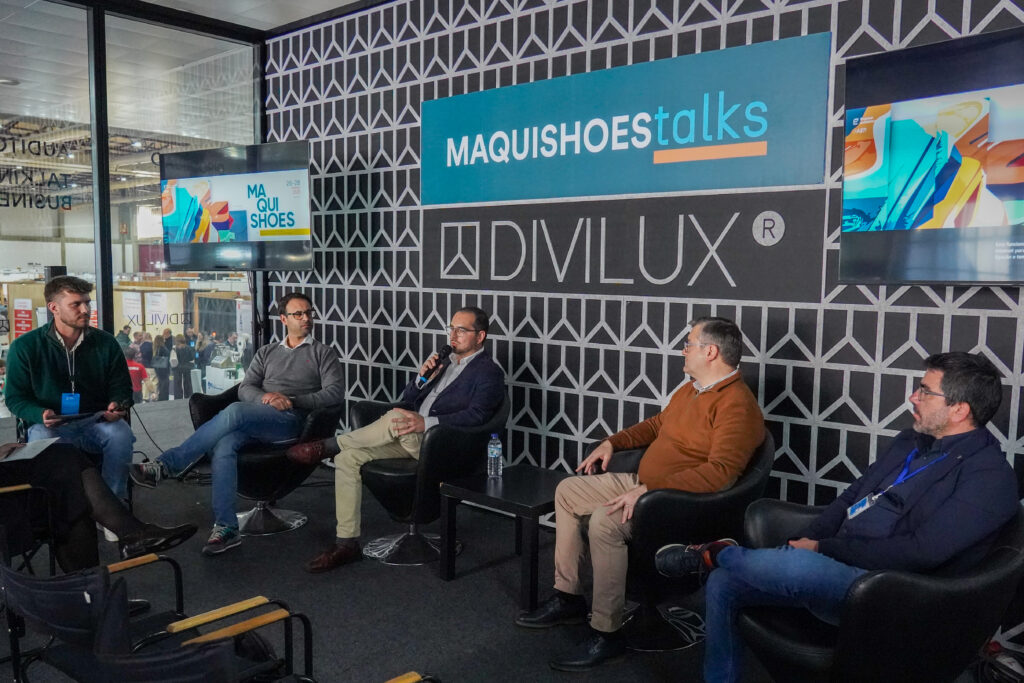
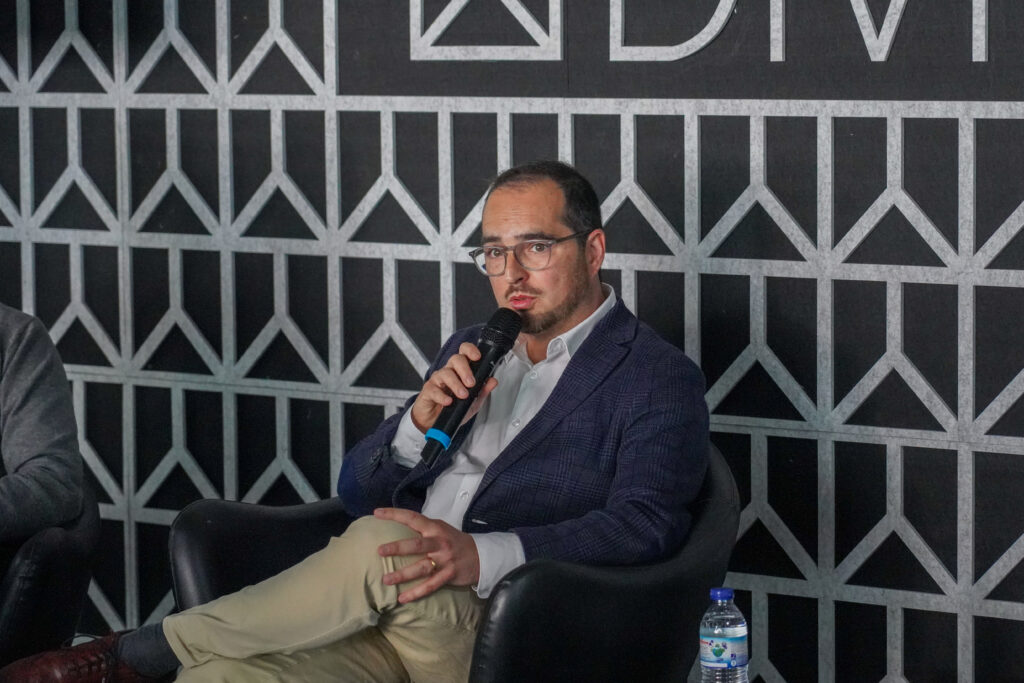
Gratitude and Commitment to the Sector
To close his contribution, Guilherme Cardoso expressed his gratitude, on behalf of JPM Industry, to the CTCP team, with special thanks to Florbela Silva, Cristiano Figueiredo, and Pedro Duarte, who initially extended the invitation, as well as to the companies that collaborated within the scope of the FAIST project, highlighting the spirit of cooperation that defines the industry.
JPM Industry’s participation in Maquishoes reinforces its commitment to technological innovation, intercompany collaboration, and the development of solutions that drive a more efficient, flexible, and competitive footwear industry.